****************nano vna user guide****************
NanoVNA User Guide
- Introduction
- First thing to do
- input method
- How to read the screen
- Start measurement
- Calibration method
- function
- How to update the firmware
- Firmware Development Guide
- Example of use
Introduction
This document is an unofficial user guide for NanoVNA. The URL is https://cho45.github.io/NanoVNA-manual/
Please send a Pull-request if you have any changes, such as a conflict with the latest firmware.
It is also available in PDF format on the GitHub Releases page.
- https://github.com/cho45/NanoVNA-manual/releases
What is NanoVNA
There are several types of hardware for NanoVNA, and this document covers the following hardware:
- ttrftech version (original) ttrftech / NanoVNA
- hugen79 version hugen79 / NanoVNA-H
These hardware have similar components on the circuit and common firmware is available.
What you need to work
At a minimum, you need:
- NanoVNA body
- SMA LOAD 50Ω
- SMA SHORT
- SMA OPEN
- SMA Female to Female Through Connector
- SMA Male to Male cable × 2
NanoVNA Basics
VNA (Vector Network Analyzer) measures the frequency characteristics of reflected power and transmitted power of a radio frequency network (RF Network).
NanoVNA measures the following factors:
- Input voltage I / Q signal
- I / Q signal of reflected voltage
- I / Q signal of passing voltage
From this we calculate:
- Reflection coefficients S11
- Transmission coefficient S21
The following items that can be calculated from these can be displayed.
- Return loss
- Passage loss
- Complex impedance
- resistance
- reactance
- SWR
Such.
Oscillation frequency of NanoVNA
The NanoVNA measures the reflection coefficient and transmission coefficient for 101 points in the frequency band to be measured.
The local frequency of NanoVNA is from 50kHz to 300MHz. Higher frequencies use harmonic mode. The fundamental wave is not attenuated even in the harmonic mode. The usage modes for each frequency are as follows.
- Up to 300 MHz: fundamental wave
- 300MHz to 900MHz: 3rd harmonic
- 900MHz to 1500MHz: 5th harmonic
Especially when checking the gain of the amplifier, it is necessary to pay attention to the fact that there is always a fundamental wave input.
The input is converted to an intermediate frequency of 5 kHz in each case. The signal is converted from analog to digital at 48kHz sampling. Digital data is processed by the MCU.
First thing to do
It must be calibrated first before it can be used. Initially, calibrate as follows.
- Make sure START is 50kHz
- Confirm that STOP is 900MHz
- Perform calibration according to the calibration method
input method
The NanoVNA has the following inputs:
- Tap and long tap on touch panel
- Lever switch
- L / L Long press
- R / R Long press
- Press / Press and hold
- Power slide switch
How to read the screen
Main screen
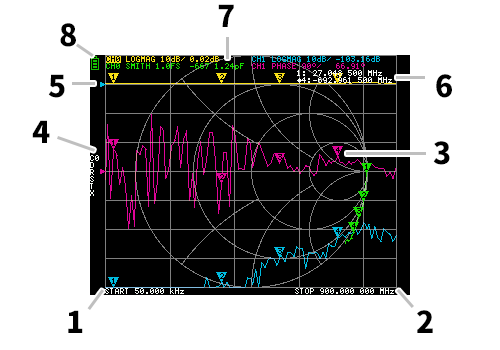
1. START 2. STOP frequency
Each frequency when the start / stop is specified is displayed.
3. Markers
The position of the marker for each trace is displayed. The selected marker can be moved in the following ways.
- Drag marker on touch panel
- Long press LR on lever switch
4. Calibration status
Displays the data number of the calibration being read and the error correction applied.
C0
C1
C2
C3
C4
: Indicates that the corresponding number of calibration data is loaded.c0
c1
c2
c3
c4
: Each indicates that the corresponding number of calibration data has been loaded, but indicates that the frequency range has been changed after loading and interpolation is used for error correction.D
: Indicates that directivity error correction is appliedR
: Indicates that refrection tracking error correction is appliedS
: Indicates that source match error correction is appliedT
: Indicates that transmission tracking error correction has been appliedX
: Indicates that isolation (crosstalk) error correction has been applied
5. Reference position
Indicates the reference position of the corresponding trace. You can change the position with
DISPLAY
SCALE
REFERENCE POSITION
.6. Marker status
The active marker you selected and one previously active marker are displayed.
7. Trace status
The status of each trace format and the value corresponding to the active marker are displayed.
For example, if the display is
CH0 LOGMAG 10dB/ 0.02dB
, read as follows.- Channel CH0 (reflection)
- Format
LOGMAG
- Scale is 10dB
- Current value is 0.02dB
The channel display of the active trace is inverted.
8. Battery status
If the battery is installed and
D2
on the PCB is already mounted, the icon will be displayed according to the battery voltage.Main screen 2
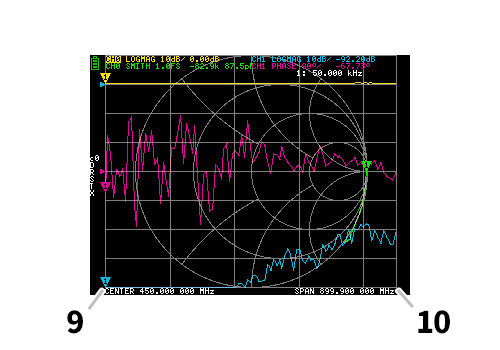
9. CENTER frequency 10. Span
The respective frequencies when the center frequency and span are specified are displayed.
Menu screen
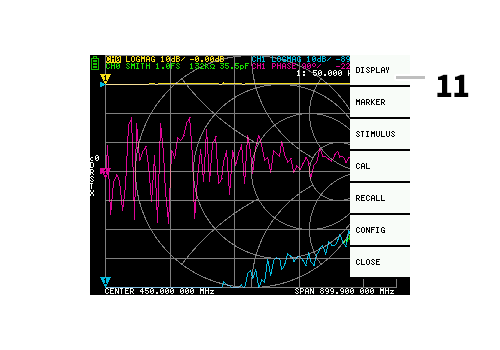
11. Menu
The menu can be displayed by the following operations.
- When you tap anywhere other than the marker on the touch panel
- Push the lever switch
Keypad screen
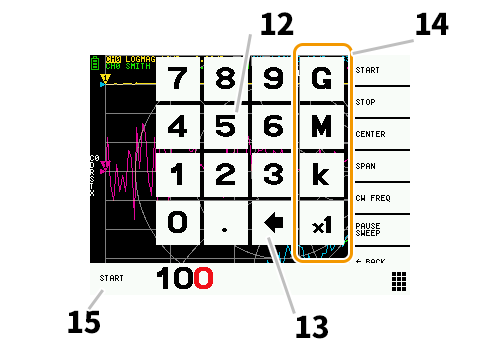
12. Numeric keys
Tap a number to enter one character.
13. Back key
Delete one character. If no characters have been entered, cancel the entry and return to the previous state.
14. Unit key
Multiplies the current input by the appropriate unit and terminates the input immediately. In the case of × 1, the entered value is set as it is.
15. Input field
The input target item name and the entered number are displayed.
Start measurement
Basic measurement sequence
- Set the frequency range to measure
- Perform calibration
- Connect the DUT
Calibration method
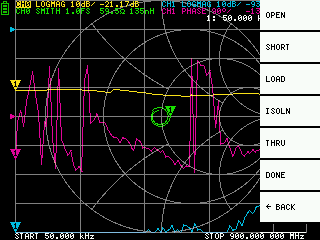
Calibration basically needs to be performed every time the frequency range to be measured is changed. If the error has been corrected correctly, the calibration status display on the screen will be
Cn DRSTX
. n is the data number being loaded.
However, NanoVNA can complement the existing calibration information and provide a somewhat correct display. This happens if you change the frequency range after loading the calibration data. At this time, the display of the calibration status on the screen is
cn DRSTX
. n is the data number being loaded.- Resets the current calibration status
CAL
RESET
- Connect OPEN standard to CH0 port and execute
CAL
CALIBRATE
OPEN
. - Connect SHORT standard to CH0 port and execute
CAL
CALIBRATE
SHORT
. - Connect LOAD standard to CH0 port and execute
CAL
CALIBRATE
LOAD
. - Connect LOAD standard to CH0 and CH1 ports and execute
CAL
CALIBRATE
ISOLN
. If there is only one load, the CH0 port can be left unconnected. - Connect the cables to the CH0 and CH1 ports, connect the cables with through connectors, and execute
CAL
CALIBRATE
THRU
. - Finish calibration and calculate error correction information
CAL
CALIBRATE
DONE
- Specify the data number and save.
CAL
CALIBRATE
SAVE
SAVE 0
* It is necessary to import each calibration data after the display is sufficiently stable.
function
Trace display
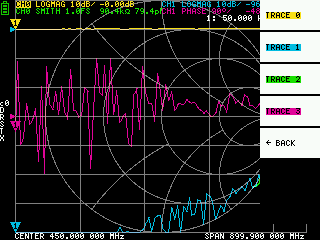
Up to four traces can be displayed, one of which is the active trace.
Traces show only what you need. To switch the display, select
DISPLAY
TRACE
TRACE n
.
There are the following ways to switch the active trace.
- Tap the marker of the trace you want to activate
- Select and display
DISPLAY
TRACE
TRACE n
. (If it is already displayed, you need to temporarily hide it)
Trace format
Each trace can have its own format. To change the format of the active trace
DISPLAY
FORMAT
Select the format you want to change.
The display of each format is as follows.
LOGMAG
: Logarithm of absolute value of measured valuePHASE
: Phase from -180 ° to + 180 °DELAY
: DelaySMITH
: Smith chartSWR
: Standing Wave RatioPOLAR
: polar coordinate formatLINEAR
: Absolute value of measured valueREAL
: Real number of measured valueIMAG
: Imaginary number of measured valueRESISTANCE
: The resistance component of the measured impedanceREACTANCE
: The reactance component of the measured impedance
Trace channel
The NanoVNA has two ports,
CH0
CH1
. The following S parameters can be measured for each port.CH0
S11 (CH0
loss)CH1
S21 (insertion loss)
To change the trace channel, select
CH0 REFLECT
or CH1 THROUGH
of DISPLAY
CHANNEL
.marker
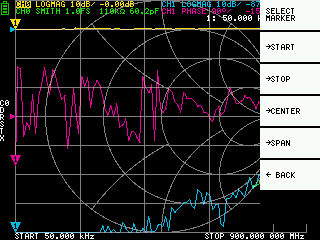
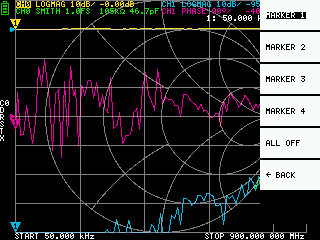
Up to four markers can be displayed. Markers are displayed from
MARKER
SELECT MARKER
MARKER n
. When you display a marker, the active marker is set to the displayed marker.Time domain operation
The NanoVNA can simulate time domain measurements by processing the frequency domain data.
To convert measurement data to the time domain, select
DISPLAY
TRANSOFRM
TRANSFORM ON
. TRANSFORM ON
is enabled, the measurement data is immediately converted to the time domain and displayed.
The following relationship exists between the time domain and the frequency domain.
- Increasing the maximum frequency increases the time resolution
- The shorter the measurement frequency interval (ie, the lower the maximum frequency), the longer the maximum time length
Therefore, there is a trade-off between the maximum time length and the time resolution.
To translate the length of time into distance, the following can be said.
- If you want to increase the maximum measurement distance, you need to lower the maximum frequency
- If you want to specify the distance accurately, you need to increase the maximum frequency.
Time domain bandpass
In bandpass mode, you can simulate the response of the DUT to an impulse signal.
The trace format can be set to
LINEAR
LOGMAG
SWR
.
Below is an example of the impulse response of a bandpass filter.
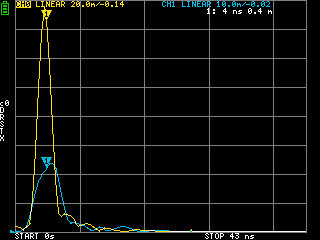
Time domain low pass impulse
In low-pass mode, you can simulate TDR. In low-pass mode, the start frequency must be set to 50kHz and the stop frequency must be set according to the distance to be measured.
Trace format can be set to
REAL
.
The following shows an example of the step response in the open state and the impulse response in the short state.
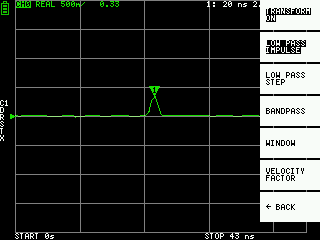
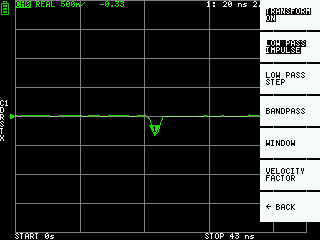
Time domain low pass step
In low-pass mode, you can simulate TDR. In low-pass mode, the start frequency must be set to 50kHz and the stop frequency must be set according to the distance to be measured.
Trace format can be set to
REAL
.
open:
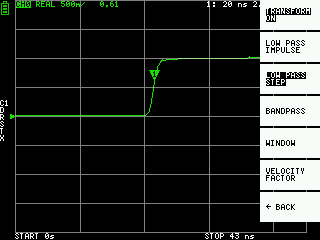
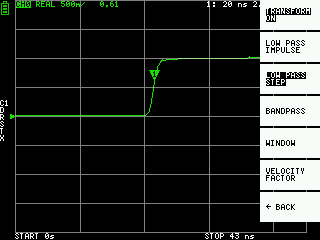
short:
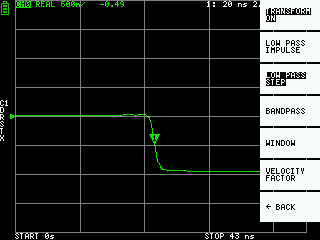
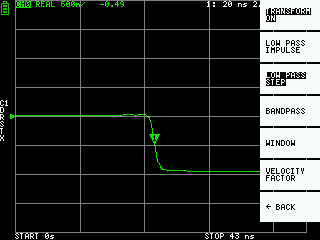
Step response example
Capacitive short:
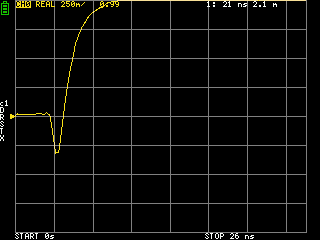
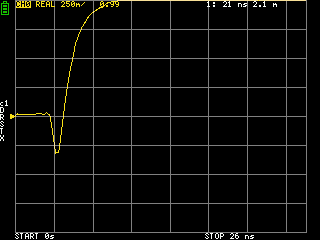
Inductive short:
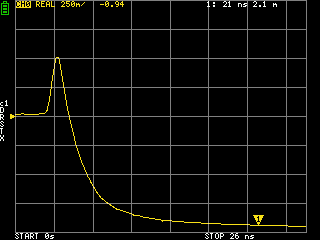
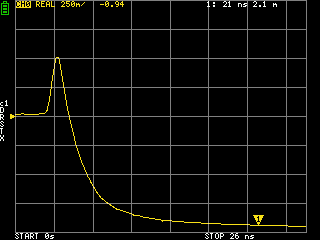
Discontinuous capacitive (C in parallel):
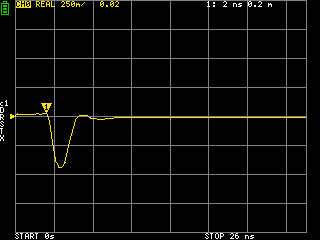
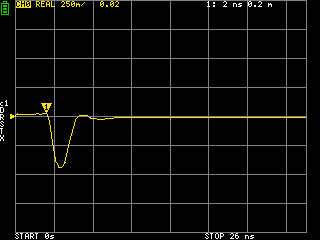
Inductive discontinuity (L in series):
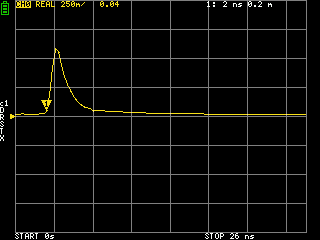
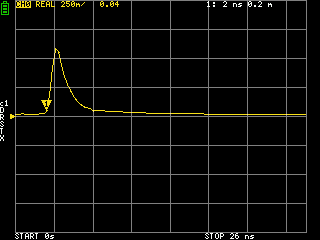
Time domain window
The measurable range is a finite number, with a minimum frequency and a maximum frequency. Windows can be used to smooth out this discontinuous measurement data and reduce ringing.
There are three levels of windows.
- MINIMUM (no window, ie same as rectangular window)
- NORMAL (equivalent to β = 6 in Kaiser window)
- MAXIMUM (equivalent to β = 13 in Kaiser window)
MINIMUM has the highest resolution and MAXIMUM has the highest dynamic range. NORMAL is somewhere in between.
Setting the Velocity Factor in the time domain
The transmission speed of electromagnetic waves in a cable depends on its material. The ratio of electromagnetic wave transmission speed in a vacuum to wavelength transmission rate (Velocity Factor, Velocity of propagation) is called. This is always stated in the cable specifications.
In the time domain, the displayed time can be converted to distance. The wavelength reduction rate used for distance display can be set with
DISPLAY
TRANSFORM
VELOCITY FACTOR
. For example, if you measure the TDR of a cable that has a 67% wavelength reduction ratio, specify 67
in the VELOCITY FACTOR
.Set frequency from marker
You can set the frequency range from the marker as follows.
MARKER
→START
Set the frequency of the active marker to the start frequencyMARKER
→STOP
Sets the frequency of the active marker to the stop frequencyMARKER
→CENTER
Sets the active marker frequency to the center frequency. The span is adjusted to maintain the current range as much as possible.MARKER
→SPAN
Set the two displayed markers, including the active marker, to the span. Nothing happens if only one marker is displayed.
Setting the measurement range
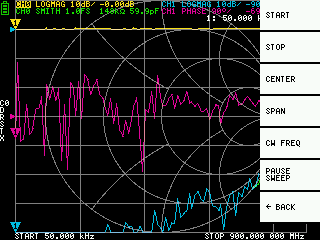
There are three types of measurement range settings.
- Set the start frequency and stop frequency
- Set center frequency and span
- Zero span
Set the start frequency and stop frequency
Select and set
STIMULUS
START
and STIMULUS
STOP
, respectively.Set center frequency and span
Select and set
STIMULUS
CENTER
and STIMULUS
SPAN
respectively.Zero span
Zero span is a mode in which one frequency is transmitted continuously without performing a frequency sweep.
Select and set
STIMULUS
CW FREQ
.Stop measurement temporarily
Selecting
STIMULUS
PAUSE SWEEP
temporarily stops measurement.Recall calibration and settings
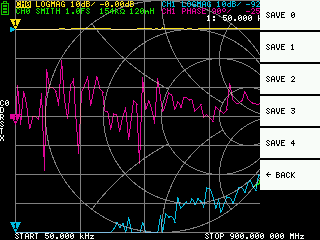
Up to five calibration data can be stored. Immediately after NanoVNA starts, it loads the data with number 0.
Calibration data is data that contains the following information:
- Frequency setting range
- Error correction at each measurement point
- Trace setting status
- Marker setting status
- Domain mode settings
- Setting the wavelength shortening rate
- electrical delay
CAL
current settings can be saved by selecting CAL
SAVE
SAVE n
.
You can reset the current calibration data by selecting
CAL
RESET
. To re-calibrate, you need to RESET
.CAL
CORRECTION
indicates whether error correction is currently being performed. You can select this to temporarily stop error correction.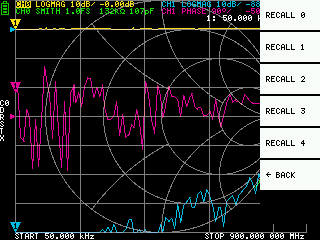
RECALL
saved settings by selecting RECALL
RECALL n
.Device settings
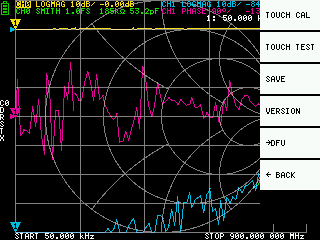
Below
CONFIG
, general settings of the device can be made.Touch panel calibration and test
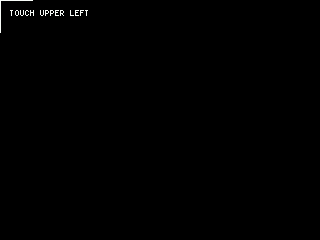
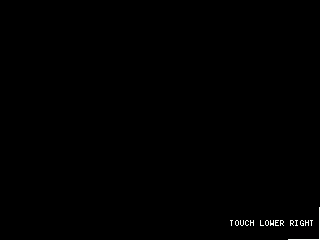
CONFIG
you select CONFIG
TOUCH CAL
, you can calibrate the touch panel. If there is a large difference between the actual tap position and the recognized tap position, this can be solved by doing so. After performing TOUCH CAL
, perform TOUCH TEST
to confirm that the settings are correct, and save the settings using SAVE
.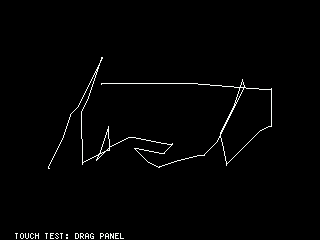
CONFIG
you select CONFIG
TOUCH TEST
, you can test the touch panel. While tapping the touch panel, a line is drawn. It returns to the original state when released from the touch panel.Saving device settings
Select
CONFIG
SAVE
to save general device settings. General device settings are data that includes the following information:- Touch panel calibration information
- Grid color
- Trace color
- Calibration data number loaded by default
There is currently no way to make settings other than touch panel calibration information.
Show version
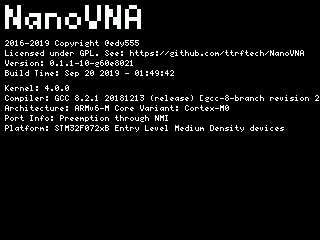
Select
CONFIG
VERSION
to display device version information.Firmware update
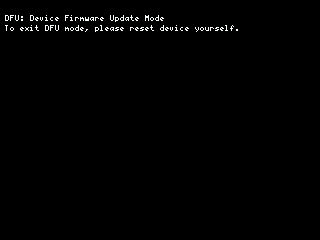
Select
CONFIG
→DFU
RESET AND ENTER DFU
to reset the device and enter DFU (Device Firmware Update) mode. In this mode, the firmware can be updated via USB.How to update the firmware
How to get the firmware
ttrftech version firmware
Original firmware. It is version controlled and is frequently developed.
GitHub releases has a somewhat stable release version of the firmware.
CircleCI has all the firmware for every commit. Use this if you want to try the latest features or check for bugs.
hugen79 version firmware
Google Drive has the latest firmware.
Build yourself
You can easily clone the github repository and build it yourself.
How to write firmware
There are various ways to write, but here we explain using dfu-util . dfu-util is a cross-platform tool, and binaries are provided on Windows, so you can use it just by downloading it.
Writing with dfu-util (Ubuntu)
There is dfu-util in the standard package repository.
sudo apt-get install dfu-util dfu-util --version
Start the device in DFU mode. Enter the DFU mode in one of the following ways.
- Turn on the power while jumping the BOOT0 pin on the PCB. (Remove the jumper after turning on the power.) The screen turns white, but it is normal.
CONFIG
→DFU
Select→DFU
RESET AND ENTER DFU
Execute the following command. build / ch.bin describes the path to the downloaded firmware file .bin.
dfu-util -d 0483:df11 -a 0 -s 0x08000000:leave -D build/ch.bin
Writing using dfu-util (macOS)
Install the brew command.
ruby -e "$(curl -fsSL https://raw.githubusercontent.com/Homebrew/install/master/install)"
Install the dfu-util command.
brew install dfu-util
Check that the dfu-util command can be started normally.
dfu-util --version
Start the device in DFU mode. Enter the DFU mode in one of the following ways.
- Turn on the power while jumping the BOOT0 pin on the PCB. (Remove the jumper after turning on the power.) The screen turns white, but it is normal.
CONFIG
→DFU
Select→DFU
RESET AND ENTER DFU
Execute the following command. build / ch.bin describes the path to the downloaded firmware file .bin.
dfu-util -d 0483:df11 -a 0 -s 0x08000000:leave -D build/ch.bin
Writing using dfu-util (Windows 10)
In Windows, when a NanoVNA in DFU mode is connected, the device driver is installed automatically. However, this device driver cannot use dfu-util. Here, the driver is exchanged using Zadig .
Start the device in DFU mode. Enter the DFU mode in one of the following ways.
- Turn on the power while jumping the BOOT0 pin on the PCB. (Remove the jumper after turning on the power.) The screen turns white, but it is normal.
CONFIG
→DFU
Select→DFU
RESET AND ENTER DFU
Start Zadig with the NanoVNA in DFU mode connected, and use WinUSB as a driver for STM32 BOOTLOADER as shown below.
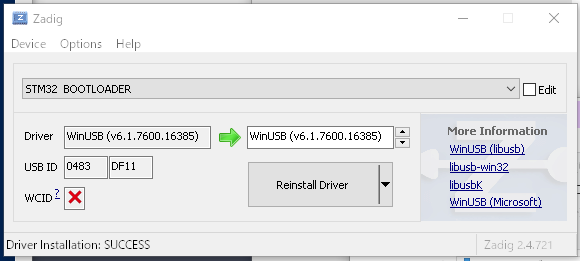
* If you want to restore the driver, search for the applicable device from "Universal Serial Bus Controller" in "Device Manager" and execute "Uninstall Device". Unplug the USB connector and plug it in again, the driver will be installed automatically.
Next, place dfu-util. Download dfu-util-0.9-win64.zip from releases and extract it. Here, it is assumed that it is expanded to C: \ dfu-util as an example (anywhere is fine).
Right-click on the start menu and select Windows PowerShell. The shell screen opens.
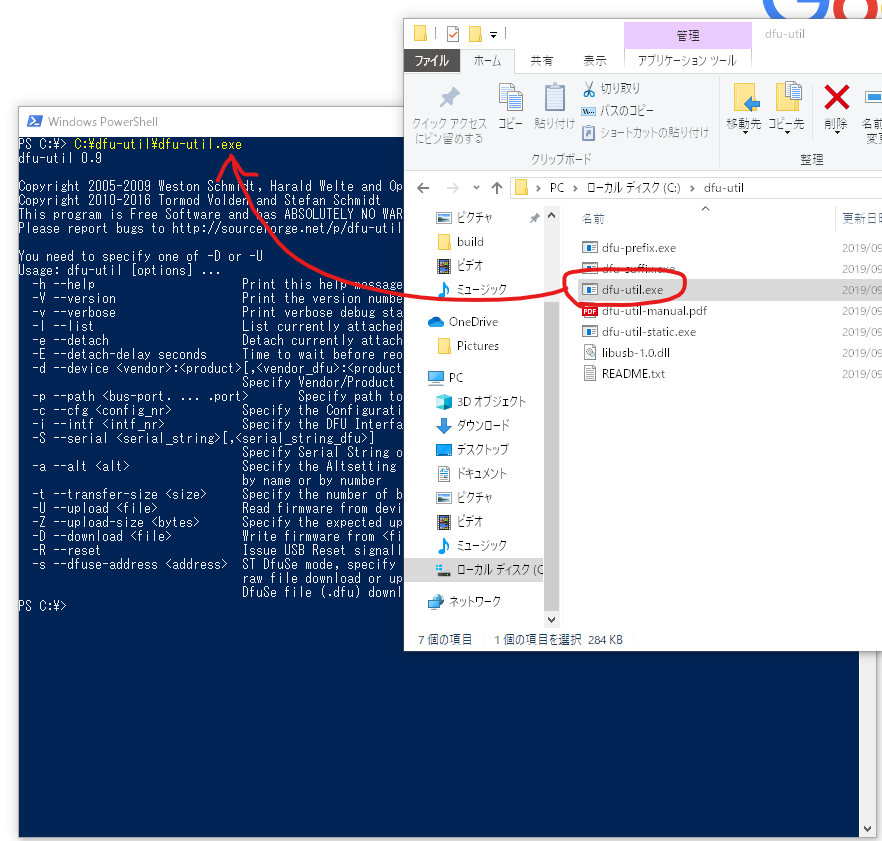
Drag and drop dfu-util.exe from Explorer to PowerShell and the path will be inserted automatically. You can display the version of dfu-util by starting with
--version
as shown below. C:\dfu-util\dfu-util.exe --version
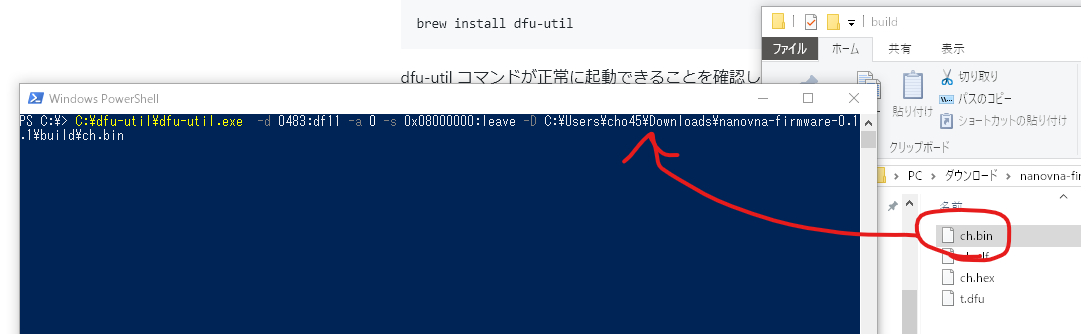
Similarly, you can enter the path of the firmware file by dragging and dropping it from Explorer to PowerShell.
Execute the following command. build / ch.bin describes the path to the downloaded firmware file .bin.
C:\dfu-util\dfu-util.exe -d 0483:df11 -a 0 -s 0x08000000:leave -D build\ch.bin
How to write firmware (Windows GUI)
For those who are unfamiliar with CUI, some complicated steps are required, but the writing method using the DfuSE Demo tool provided by ST is introduced for reference only.
Download STSW-STM32080 from the ST site .
- DFU File Manager: Tool to create .dfu files from .bin or .hex
- DfuSe Demo: Tool to write .dfu files to device
is included.
Convert file format with DFU File Manager.
First, launch DFU File Manager.
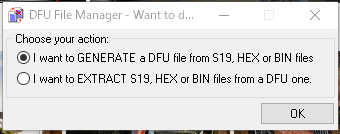
Select
I want to GENERATE a DFU file from S19, HEX or BIN files
.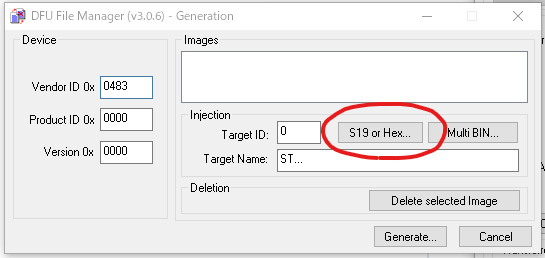
Click the
S19 or Hex...
button. ch.hex
firmware ch.hex
file, such as ch.hex
.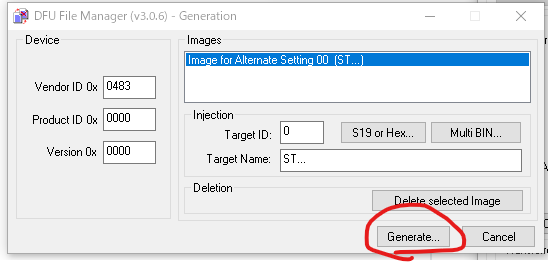
Click the
Generate...
button and create a .dfu file with a suitable name.Write firmware with DfuSe Demo
First, boot the device in DFU mode. Enter the DFU mode in one of the following ways.
- Turn on the power while jumping the BOOT0 pin on the PCB. (Remove the jumper after turning on the power.) The screen turns white, but it is normal.
CONFIG
→DFU
Select→DFU
RESET AND ENTER DFU
Start DfuSe Demo. Make sure there is
STM Device in DFU Mode
Available DFU Devices and click Choose...
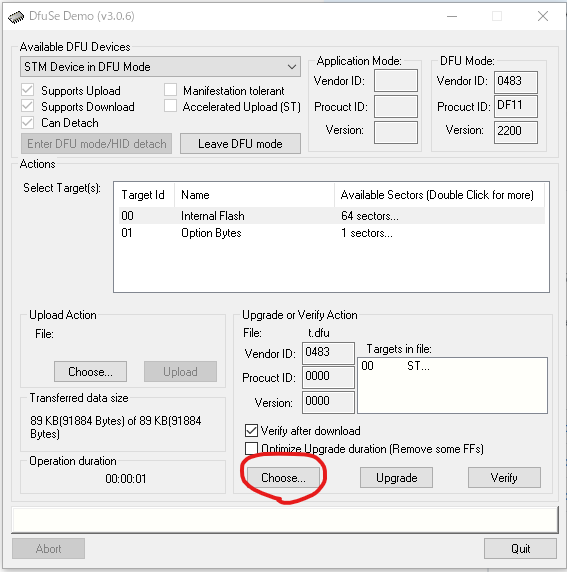
Select the .dfu file you just saved.
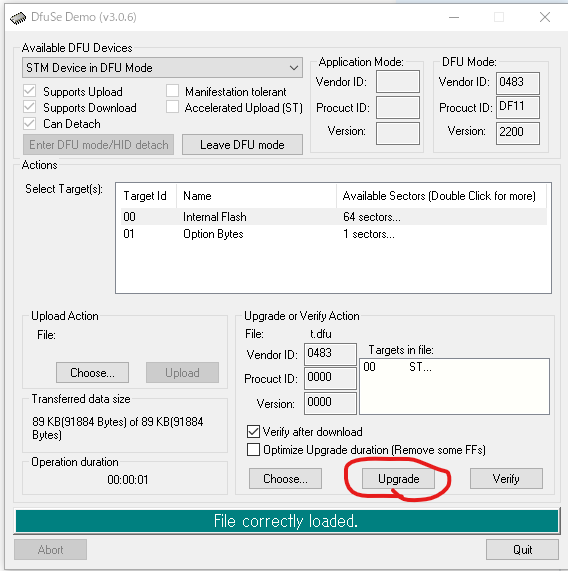
Click the
Upgrade
button.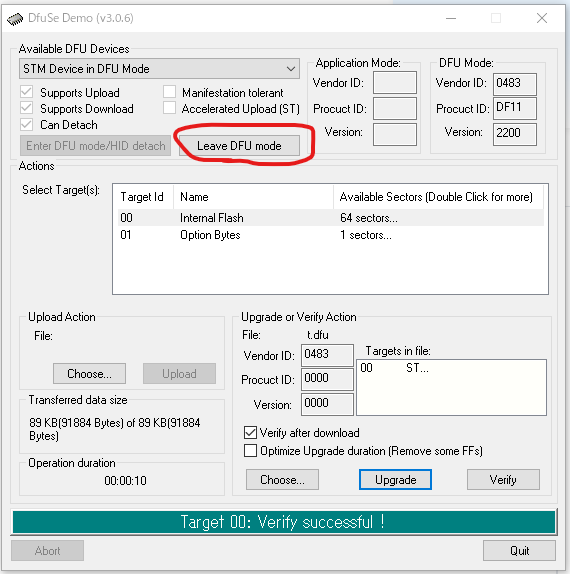
This screen will be displayed when writing is completed. Click the
Leave DFU mode
button to exit DFU mode. The device will reset and boot with the new firmware.Firmware Development Guide
The following items need to be developed for NanoVNA firmware.
- Git
- gcc-arm-none-eabi
- make
If you already have these, you can build the firmware with
make
. git clone git@github.com:ttrftech/NanoVNA.git cd NanoVNA git submodule update --init --recursive make
Build with Docker
With docker you can build without hassle. docker is a free cross-platform container utility. It can be used to quickly recreate a particular environment (in this case, a build environment).
docker run -it --rm -v $(PWD):/work edy555/arm-embedded:8.2 make
On-chip debugging with Visual Studio Code
Visual Studio Code (VSCode) is a multi-platform code editor provided by Microsoft free of charge. By installing Cortex-Debug Extension, on-chip debugging can be performed by GUI.
The platform-dependent part is omitted, but the following is required in addition to the above.
- openocd
- VSCode
- Cortex-Debug
Cortex-Debug is searched from Extensions of VSCode and installed.
tasks.json
First, define a "task" to make the entire NanoVNA on VSCode.
{
"tasks" : [
{
"type" : "shell" ,
"label" : "build" ,
"command" : "make" ,
"args" : [
],
"options" : {
"cwd" : "${workspaceRoot}"
}
}
],
"version" : "2.0.0"
}
Now you can make it as a task on VSCode.
launch.json
Next, define how it will be launched during Debug. Set as described in Cortex-Debug.
The following is the setting when using ST-Link. If you use J-Link, replace
interface/stlink.cfg
with interface/jlink.cfg
. {
"version" : "0.2.0" ,
"configurations" : [
{
"type" : "cortex-debug" ,
"servertype" : "openocd" ,
"request" : "launch" ,
"name" : "OpenOCD-Debug" ,
"executable" : "build/ch.elf" ,
"configFiles" : [
"interface/stlink.cfg" ,
"target/stm32f0x.cfg"
],
"svdFile" : "./STM32F0x8.svd" ,
"cwd" : "${workspaceRoot}" ,
"preLaunchTask" : "build" ,
}
]
}
svdFile
file specified in svdFile
can be downloaded from the ST site . svdFile
is no problem in operation even if svdFile
is not specified.Start debugging
When Start Debugging (
F5
) is performed, OpenOCD is automatically started and firmware is transferred after build by make. When the transfer is completed, a break occurs at the reset handler.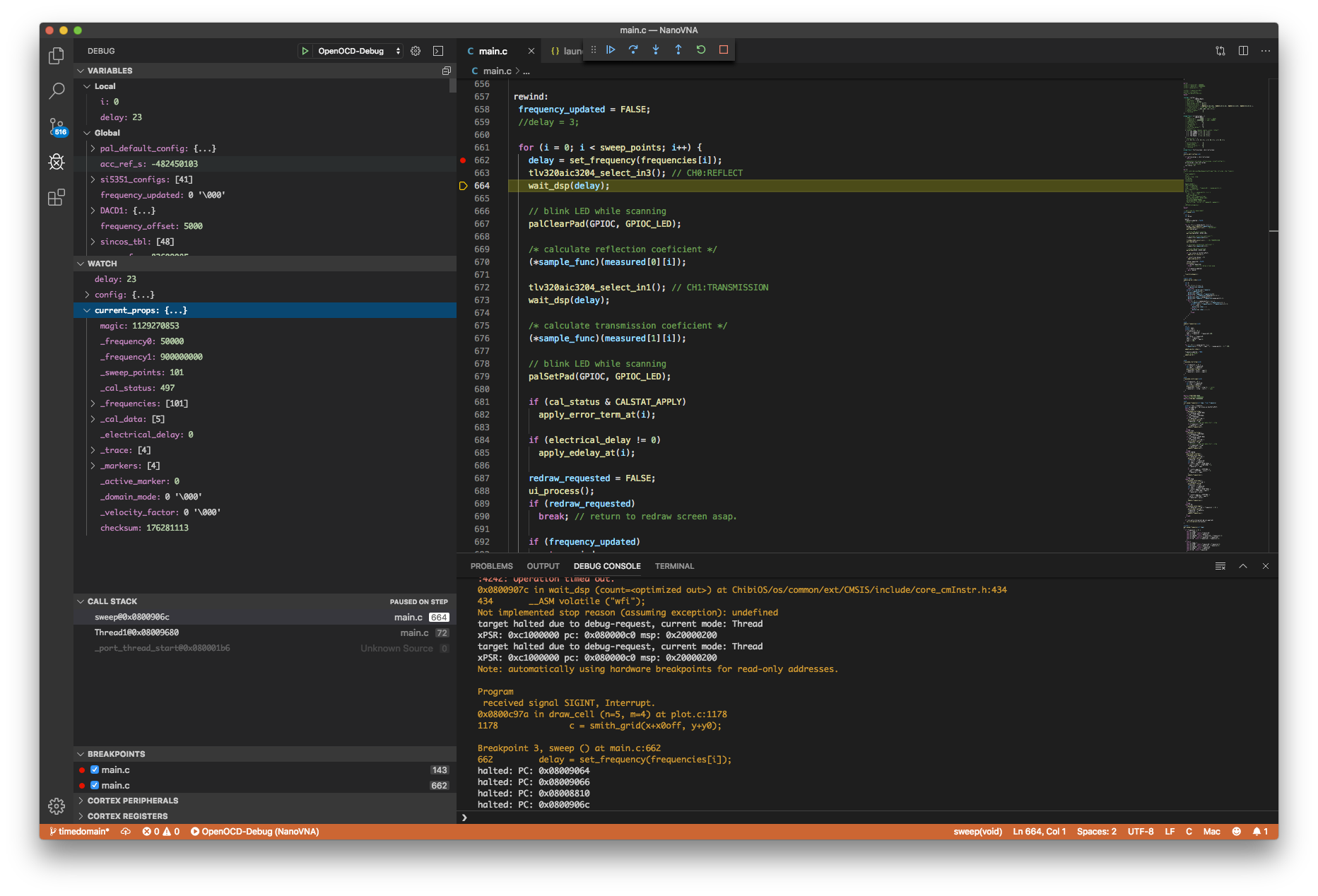
svdFile
is specified, the registers of the defined MCU are displayed on the debug screen.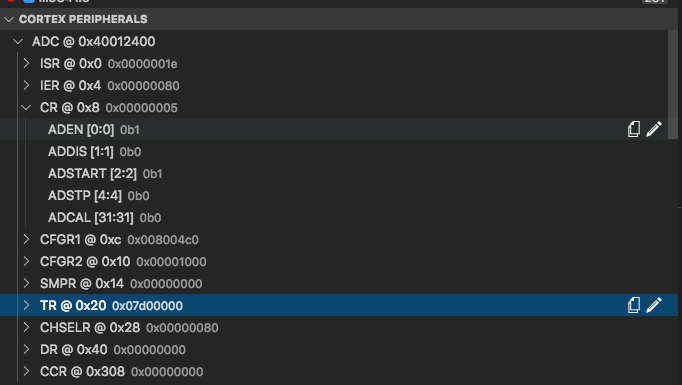
Example of use
Adjusting the bandpass filter
TODO
Adjusting the antenna
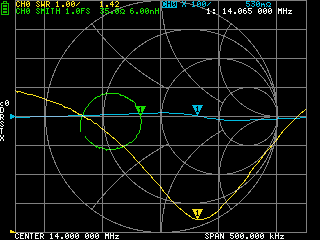
Here is an example of using NanoVNA as an antenna analyzer.
There are two important points in adjusting the antenna:
- Whether the antenna is in tune and resonance (that is, the reactance is close to 0 at the target frequency)
- Is the SWR of the antenna low (sufficient matching)
Trace settings
Since only CH0 is used for antenna adjustment, calibrate all items except
THRU
and ISOLN
.
Set the trace settings as follows.
- Trace 0: CH0 SWR
- Trace 1: CH0 REACTANCE
- Trace 2: CH0 SMITH
- Trace 3: OFF
Set the desired frequency for tuning the antenna to
CENTER
and set SPAN
appropriately.
Look for frequencies where trace 1 showing reactance is close to zero. Since the frequency is the tuning point, if it is off, adjust the antenna so that the tuning point comes to the target frequency.
If the tuning point is at the desired frequency, check that Trace 0, which is displaying SWR, is displaying a sufficiently low (close to 1) SWR. If it does not show enough (less than 2) SWR, it will be matched using a Smith chart. In this case, matching may be performed using an antenna tuner directly below the antenna.
If the SWR drops, you are tuned to the desired frequency and you are finished tuning the low SWR antenna.
Check cable
You can simulate TDR by using the low-pass mode in the time domain. By using TDR, it is possible to detect transmission line defects.
TODO
Common mode filter measurement
TODO
*************************************************